Recycled Steel Making- The Future of Building
- Stu McWilliams
- Mar 28, 2024
- 9 min read
When you think of steel making, the word "Green" doesn't necessarily come to the front of mind. However, due to advances in steel making efficiency and a lot of hard work on the scrap recollection and recovery side, modern circular steel production is one of the greenest ways to build today. Let's uncover the economic advantages, ecological benefits, and promising future prospects that recycled steel offers. From reducing carbon emissions to preserving natural resources, recycled steel emerges as a beacon of hope for a greener, more resilient future. So, join us as we embark on a quest to understand the power of recycled steel—where scrap becomes strength, and sustainability becomes reality.
Steel stands as the backbone of modern civilization, omnipresent in buildings, infrastructure, vehicles, and countless everyday objects. Its unparalleled strength, versatility, and durability have cemented its status as a cornerstone material in construction, manufacturing, and beyond.
While steel's indispensability is undeniable, so too are the environmental and economic challenges posed by its production. Enter recycled steel production, a transformative process that reimagines steelmaking by harnessing the power of recycling. This blog explores the journey from scrap to strength, contrasting traditional steelmaking methods with the innovative practices of recycled steel production.

This exploration will delve into the intricate processes of traditional steelmaking, juxtaposed against the efficiency and sustainability of recycled steel production. Moreover, it will illuminate the economic advantages and ecological benefits that recycled steel offers. Recycled Steel making is the future of building and Peak Building Systems is proud to be a part of it.
Traditional or "Extractive" Steel Production
Extractive steelmaking begins with iron ore extraction and concentration, followed by smelting in blast furnaces with coke and limestone to produce pig iron. Pig iron is then refined in oxygen or electric arc furnaces, alloyed with elements like carbon and manganese, and shaped into steel products. This energy-intensive process generates emissions, prompting the search for sustainable alternatives such as recycled steel production. This method accounts for approximately 70% of global steel production according to Nucor. For More Information on this process, check out our more detailed blog here.
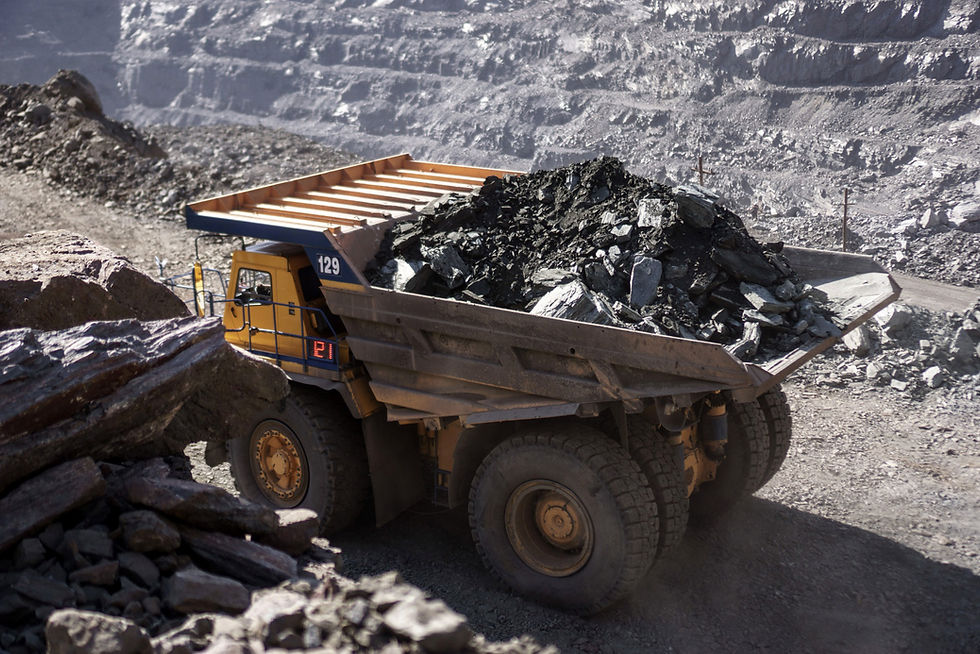
Iron Ore Extraction: Mining operations extract iron ore from deposits found in various regions worldwide.
Iron Smelting: Iron ore is smelted in blast furnaces, where it undergoes high-temperature reactions to produce molten iron, known as pig iron.
Steelmaking: Pig iron is then refined and transformed into steel through processes such as the basic oxygen process (BOP) or the electric arc furnace (EAF) method.
Alloying and Forming: Steel undergoes further refining and alloying to achieve desired properties, followed by shaping into sheets, bars, or other forms.
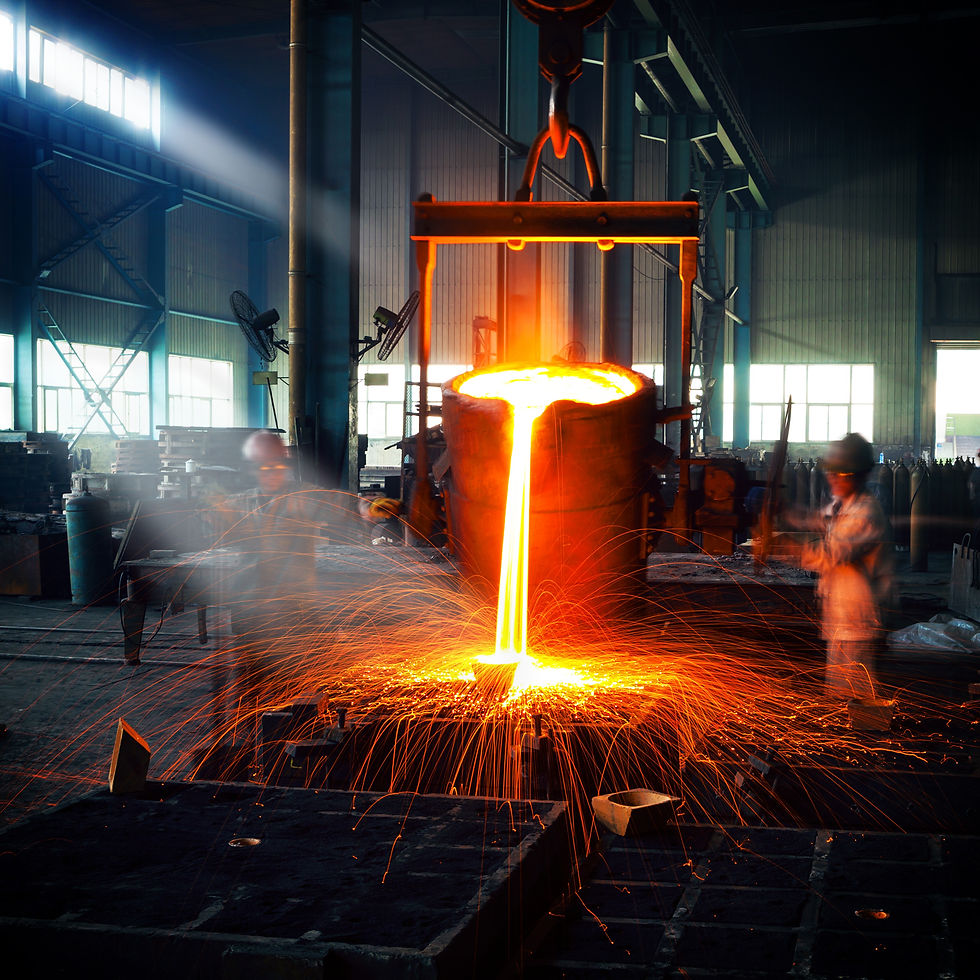
Environmental Impact of Traditional Steelmaking
Traditional steelmaking processes are notorious for their significant environmental footprint. Emissions of greenhouse gases, including carbon dioxide and sulfur dioxide, contribute to air pollution and climate change. Additionally, the extraction of raw materials and the disposal of byproducts generate various forms of pollution, impacting ecosystems and communities near steel production facilities.
Economic and Environmental Considerations Associated with Traditional Steel Production

High Capital Investment: Traditional steelmaking facilities require substantial upfront investment in infrastructure and equipment.
Volatility of Raw Material Prices: Fluctuations in the prices of iron ore, coal, and other raw materials can impact the profitability of steel production.
Energy Intensity: Traditional steelmaking is energy-intensive, leading to significant operational costs and vulnerability to energy price fluctuations.
Global Market Dynamics: Traditional steel producers face competition from domestic and international markets, influencing pricing strategies and market share.
Environmental Impacts: Extractive steelmaking processes contribute to significant environmental impacts, including emissions of greenhouse gases and pollution associated with raw material extraction and waste disposal.
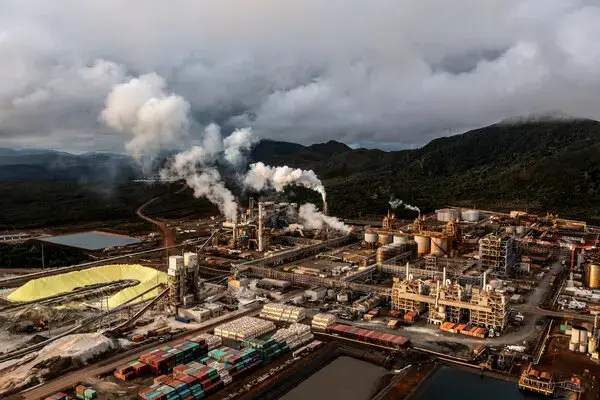
Understanding these aspects of traditional steelmaking sets the stage for exploring the alternative paradigm of recycled steel production and its potential to address the challenges faced by the steel industry.
The Rise of Recycled Steelmaking
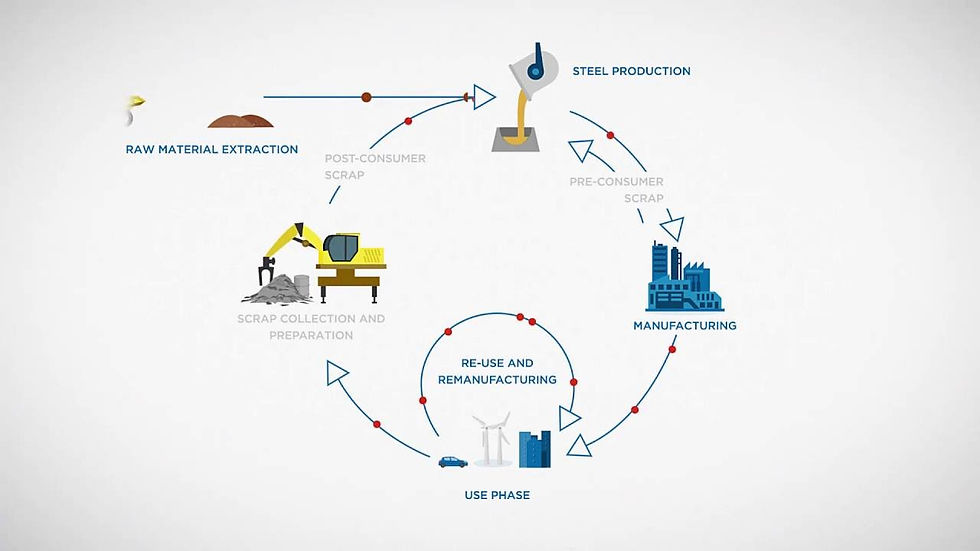
Recycled steel production represents a paradigm shift in the steelmaking industry, offering a sustainable alternative to traditional methods. At its core, recycled steel production involves the collection, processing, and remelting of scrap steel materials to create new steel products. This approach reduces reliance on virgin raw materials and minimizes waste, making it a much more environmentally friendly option. Here in the United States, this method accounts for 70% of the steel produced here. Nucor leads the way domestically as the top recycler anywhere in the western Hemisphere. Since Peak Buildings Systems is an Authorized Builder with American Buildings, A Nucor Brand, our customers can rest assured that each building we sell is made with recycled steel.
How Recycled Steel is Sourced and Processed

Collection of Scrap: Recycled steel begins its journey as scrap metal sourced from various post-consumer and industrial sources, including automobiles, appliances, and construction materials.
Sorting and Preparation: Scrap metal undergoes sorting and processing to remove contaminants and segregate different types of metals.
Melting and Refining: Cleaned scrap metal is melted in electric arc furnaces or induction furnaces, where it is refined to remove impurities and achieve desired chemical compositions.
Casting and Forming: Molten steel is cast into ingots, slabs, or billets, which are then formed into final products through rolling, forging, or other shaping processes.
Comparison of Energy Consumption and Emissions
Recycled steel production offers several environmental advantages over traditional methods, primarily due to reduced energy consumption and emissions. Unlike traditional steelmaking, which relies on the extraction and processing of raw materials, recycled steel production predominantly utilizes scrap metal as its feedstock. As a result, it requires less energy and generates fewer emissions associated with mining, transportation, and refining of raw materials.
Technological Advancements Driving Growth
Advancements in technology have played a pivotal role in driving the growth of recycled steel production. Innovations in scrap metal processing, furnace design, and energy efficiency have enabled recycled steel producers to enhance productivity, reduce costs, and improve environmental performance. Additionally, the adoption of digital technologies and automation has streamlined operations and optimized resource utilization in recycled steel plants.
Understanding the evolution and benefits of recycled steel production underscores its potential to revolutionize the steelmaking industry, paving the way for a more sustainable and resilient future.
Economic Benefits of Recycled Steel
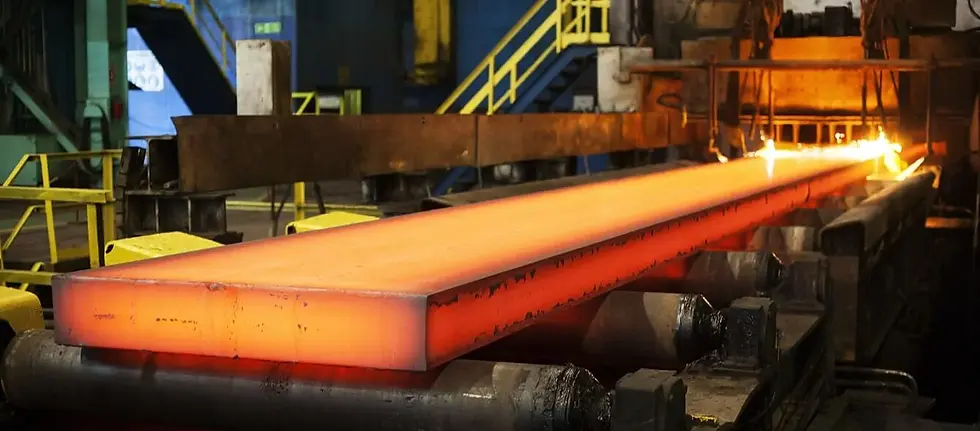
Cost-Effectiveness of Using Recycled Steel in Manufacturing
Recycled steel offers compelling economic advantages for manufacturers across various industries. Compared to traditional steel made from virgin raw materials, recycled steel often boasts lower production costs. The utilization of scrap metal as the primary feedstock eliminates the need for costly mining, transportation, and processing of raw materials. As a result, manufacturers can achieve significant cost savings in their production processes, enhancing their competitiveness in the market.
Savings in Energy and Raw Material Costs
One of the most significant economic benefits of recycled steel production is its reduced energy consumption and lower reliance on raw materials. Traditional steelmaking consumes vast amounts of energy and resources in the extraction, processing, and refining of iron ore and other raw materials. In contrast, recycled steel production primarily utilizes scrap metal, which requires less energy and processing to convert into usable steel products. By minimizing energy and raw material costs, recycled steel producers can achieve greater efficiency and profitability in their operations.
Job Creation and Economic Opportunities
The growth of the recycled steel industry also presents significant opportunities for job creation and economic development. As demand for recycled steel continues to rise, so too does the need for skilled workers in various roles, including scrap metal collection, processing, and steel manufacturing. Moreover, the expansion of recycled steel production stimulates economic activity in related industries, such as transportation, logistics, and equipment manufacturing. By fostering job creation and economic opportunities, recycled steel contributes to vibrant and sustainable communities.
Impact on Global Steel Markets and Trade
The increasing adoption of recycled steel has implications for global steel markets and trade dynamics. As more manufacturers prioritize sustainability and environmental responsibility, the demand for recycled steel is expected to grow steadily. This trend could reshape the competitive landscape of the steel industry, leading to changes in pricing, market share, and trade patterns. Additionally, the expansion of recycled steel production may reduce dependence on imported raw materials, enhancing national and regional self-sufficiency in steel production.
By capitalizing on the economic benefits of recycled steel, manufacturers can not only improve their bottom line but also contribute to a more sustainable and resilient economy. Embracing recycled steel production offers a win-win solution that combines environmental stewardship with economic prosperity.
Ecological Advantages of Recycled Steel
Reduction of Carbon Emissions and Environmental Footprint
Recycled steel production offers significant environmental benefits, particularly in reducing carbon emissions and minimizing environmental footprint. Unlike traditional steelmaking, which relies heavily on fossil fuels and emits substantial greenhouse gases, recycled steel production consumes less energy and generates fewer emissions. By using scrap metal as the primary feedstock, recycled steel plants contribute to lower carbon intensity and help mitigate climate change. Additionally, the reduction in energy consumption and emissions associated with recycled steel production contributes to cleaner air and water, improving overall environmental quality.
Preservation of Natural Resources Through Recycling
One of the fundamental principles of recycled steel production is resource conservation through recycling. By repurposing scrap metal instead of extracting virgin raw materials, recycled steel production helps preserve natural resources such as iron ore, coal, and limestone. This conservation of resources not only extends the lifespan of finite resources but also reduces the environmental impact of resource extraction, including habitat destruction, land degradation, and water pollution. Moreover, recycling steel minimizes the need for landfill space, alleviating pressure on waste management systems and reducing the risk of environmental contamination.
Mitigation of Waste Disposal Issues
Steel recycling plays a crucial role in mitigating waste disposal issues by diverting scrap metal from landfills and incinerators. Steel is one of the most recycled materials globally, with high recycling rates achieved through efficient collection, processing, and reuse infrastructure. By recycling steel scrap into new products, recycled steel production reduces the volume of waste sent to landfills and minimizes the environmental risks associated with waste disposal, such as leachate contamination and greenhouse gas emissions. Additionally, recycling steel helps close the loop on the circular economy, promoting resource efficiency and waste reduction throughout the product lifecycle.
Contribution to Sustainable Development Goals
The ecological advantages of recycled steel align closely with the principles of sustainable development, as outlined in the United Nations Sustainable Development Goals (SDGs). Recycled steel production contributes to several SDGs, including Goal 7 (Affordable and Clean Energy), Goal 12 (Responsible Consumption and Production), and Goal 13 (Climate Action). By promoting energy efficiency, resource conservation, and environmental stewardship, recycled steel plays a vital role in advancing sustainable development objectives at the global, national, and local levels.
Through its ecological advantages, recycled steel production offers a compelling solution to environmental challenges while supporting sustainable development goals and creating a more resilient future for generations to come.

Challenges and Future Prospects
Challenges Faced by the Recycled Steel Industry
Quality Control: Maintaining consistent quality standards poses a challenge in recycled steel production due to variations in scrap composition and contamination.
Infrastructure Investment: Developing and upgrading recycling infrastructure requires significant investment in collection, processing, and remelting facilities.
Market Dynamics: Recycled steel producers must navigate market fluctuations and competition from traditional steel producers, as well as global trade dynamics.
Technological Innovation: Continuous innovation is essential to address technological barriers and improve efficiency in recycled steel production processes.
Potential Technological Innovations
Advanced Sorting Technologies: Innovations in sensor-based sorting systems can enhance the efficiency and accuracy of scrap metal sorting, improving material quality and reducing processing costs.
Clean Steelmaking Technologies: Development of advanced melting and refining technologies, such as plasma arc furnaces and hydrogen-based processes, can further reduce emissions and energy consumption in recycled steel production.
Digitalization and Automation: Integration of digital technologies and automation systems can optimize plant operations, enhance resource efficiency, and streamline production processes in recycled steel plants.
Future Trends and Growth Prospects
Rising Demand for Sustainable Materials: Growing awareness of environmental issues and sustainability concerns among consumers and industries is expected to drive increased demand for recycled steel.
Policy Support and Regulation: Government policies and regulations aimed at promoting recycling, reducing carbon emissions, and fostering sustainable development are likely to create favorable conditions for the growth of the recycled steel industry.
Circular Economy Initiatives: Adoption of circular economy principles by businesses and governments worldwide will emphasize the importance of recycling and resource conservation, further boosting demand for recycled steel.
Policy Recommendations
Investment Incentives: Governments can provide financial incentives and tax breaks to encourage investment in recycling infrastructure and technology development.
Regulatory Frameworks: Implementing regulations and standards for recycled content in steel products can create market demand and ensure quality control.
Research and Development Funding: Allocation of funding for research and development initiatives aimed at advancing recycling technologies and innovation in the steel industry can drive progress and competitiveness in the recycled steel sector.
Navigating challenges and capitalizing on opportunities will be crucial for the continued growth and success of the recycled steel industry. By addressing technological barriers, fostering innovation, and leveraging policy support, the recycled steel sector can play a pivotal role in building a more sustainable and resilient future.

Comentarios